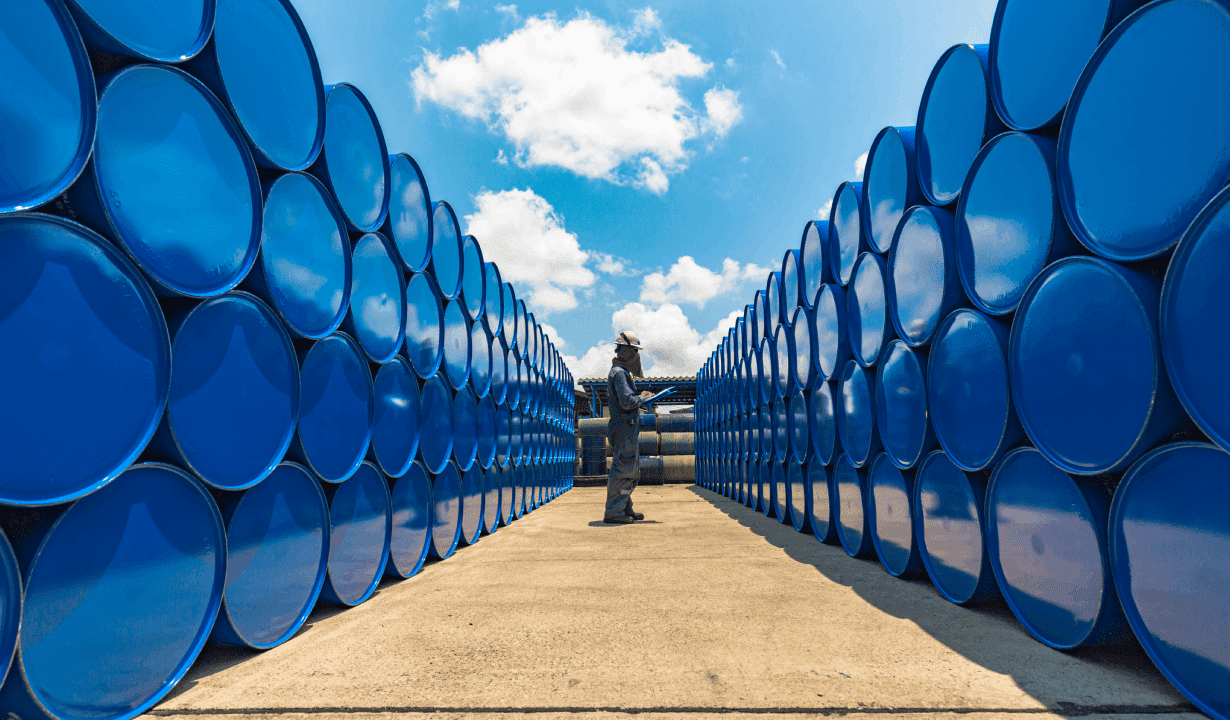
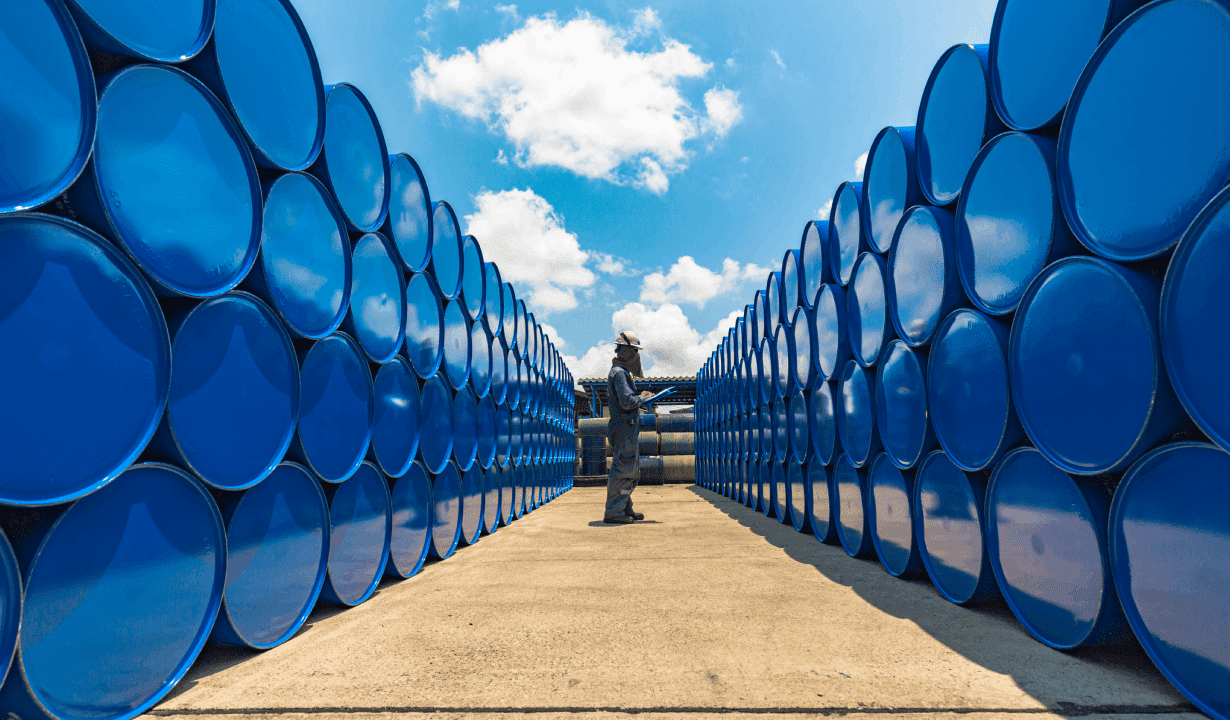
Refinery technologies have the potential to significantly reduce preventable plant losses, which are estimated to make up 80% of all losses for the oil and gas industry.
By implementing digital worker enablement technologies, implementing predictive and real-time analytics for assets and production, and creating virtual representations of physical assets, refineries can better identify the causes of lost production and create a safer working environment.
Oil and gas shipping and logistics at Aramex
80% of plant losses can be prevented with digital solutions that help capture most losses.
1 – Remote monitoring and control
Digital technologies such as IoT sensors and drones allow for remote monitoring and control of refinery assets, reducing the need for on-site inspections and maintenance. This improves safety by reducing the number of personnel required to be on site and increases efficiency by allowing for more proactive maintenance.
2 – Predictive maintenance
Machine learning algorithms can be used to analyze data from IoT sensors and other sources to predict when equipment is likely to fail. This allows for proactive maintenance to be scheduled, reducing the risk of unplanned downtime and increasing efficiency.
3 – Asset management systems
Digital asset management systems allow for the tracking and management of all refinery assets in real-time. This improves safety by ensuring that all assets are properly maintained and increases efficiency by allowing for better planning and coordination of maintenance activities.
Related article: Oil and Gas Logistics Companies Adapt to an LNG-powered Future
4 – Automation
Robotics and automation technologies can be used to automate repetitive and dangerous tasks, such as inspecting pipelines. This improves safety by reducing the risk of human error and increases efficiency by allowing for more consistent and accurate inspections.
5 – Training simulations
Virtual reality and other simulation technologies can be used to train employees in a safe and controlled environment, reducing the risk of accidents and increasing efficiency by allowing for more effective training.
6 – Digital twins
Digital twins are virtual representations of physical assets, allowing for the simulation of real-world conditions. This improves safety by allowing for testing and validation of new designs and procedures before they are implemented in the field, and increases efficiency by allowing for better planning and optimization of operations.
Related article: The Metaverse is the Future of Supply Chain Logistics
7 – Cybersecurity
Advanced cybersecurity technologies can be used to protect refinery assets from cyber attacks, improving safety by reducing the risk of disruptions and increasing efficiency by allowing for the safe and reliable operation of digital systems.
8 – Data analytics
Big data analytics can be used to gain insights from large amounts of data generated by refinery operations. This improves safety by allowing for the identification of potential risks and increases efficiency by allowing for more informed decision-making.
9 – Digital twin of the process
A digital twin of the process can be used to monitor and optimize the performance of the refinery, improving safety by reducing the risk of process upsets and increasing efficiency by allowing for better control of the process.
Related article: Can Crypto Mining Help Oil and Gas Sustainability?
10 – Remote collaboration
Digital technologies such as video conferencing and collaborative software allow for remote collaboration between teams, improving safety by reducing the need for travel and increasing efficiency by allowing for faster decision-making and problem-solving.