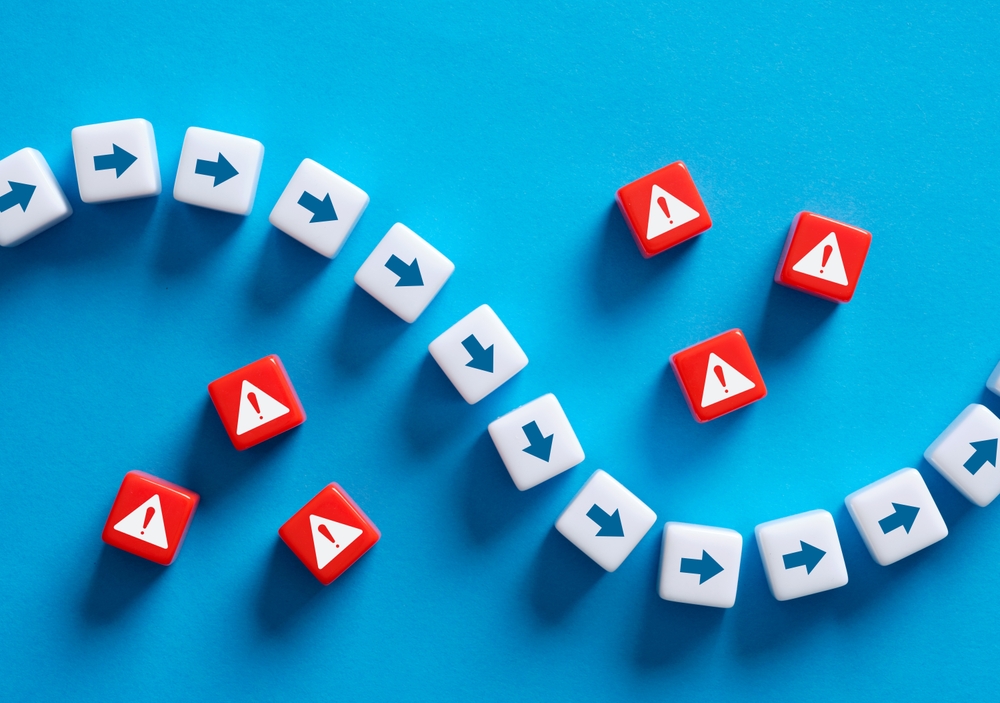
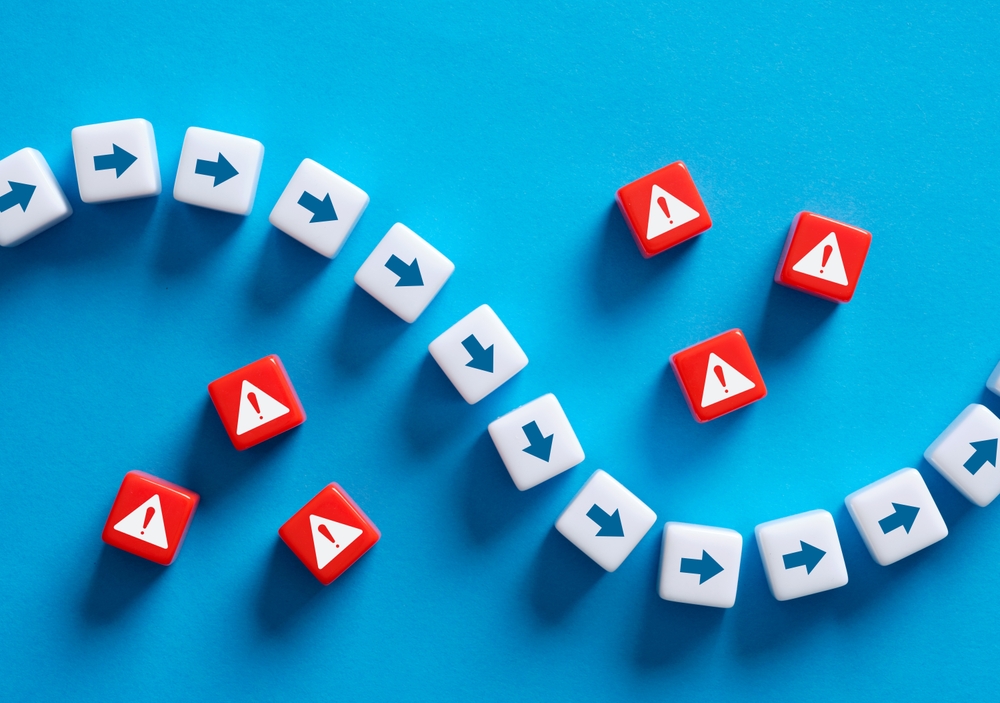
In the high-stakes chemical manufacturing business, even a minor disruption in the supply chain can cause billions in losses. It’s not just about avoiding fines or following rules anymore. Risk management strategies in logistics has become a crucial part of staying competitive. With shipping getting more complicated, regulations changing constantly, and global tensions causing chaos, businesses can’t rely on rigid systems. They need flexible, creative strategies to turn risks into opportunities.
Leading companies understand that proactive freight risk management is now a key differentiator. By leveraging predictive risk modelling, building flexible infrastructure, and staying ahead of compliance challenges, these companies gain a competitive advantage and ensure resilience in an increasingly unpredictable market.
For chemical manufacturers, risk management does not only involve being in business – it is the key to happy customers, operational sustainability, and solid market credibility. Anticipating challenges like raw material shortages, transport delays, or regulatory changes means safeguarding production and staying reliable.
Without solid risk management, disruptions can lead to steep penalties, missed deadlines, and a battered reputation. A well-rounded approach to freight forwarding and chemical shipping is essential for keeping up in this fast-paced industry.
Chemical supply chains come with their own set of unique challenges. Raw material prices are volatile, environmental regulations are stringent, and labour issues like strikes can disrupt operations. In addition, there’s always the risk of hazardous incidents, such as spills or accidents, which can have severe consequences. Together, these factors make for a complicated and unpredictable environment. Businesses need calculated strategies that prioritise resilience and compliance with industry standards to navigate it successfully.
Defining risk tolerance is another step in managing supply chain challenges. It involves deciding a business’s risk appetite, requiring senior leadership input to align with the company’s broader goals and market conditions.
Risk tolerance can vary depending on the industry and specific operational needs, but having clear limits helps guide decisions and focus efforts where they are needed most. It also ensures everyone—from executives to frontline teams—understands which risks are acceptable and require action.
A well-planned crisis management is critical to handling emergencies in chemical supply chains. It starts with having a clear strategy for incidents like spills or leaks, where everyone knows their role and what needs to happen. Quick, effective communication is equally essential—keeping employees, suppliers, and customers updated and ensuring they know what to do.
Furthermore, regular training sessions and practice drills are substantive, helping teams stay calm and focused when it matters most. Building strong connections with emergency services and regulators adds an extra layer of readiness, making it easier to tackle hazardous situations confidently.
Businesses must weave risk management into procurement, production, and distribution workflows to manage chemical supply chain risks. This means regularly assessing suppliers and logistics partners to ensure safety standards are met.
Developing a detailed risk library is another critical step—it catalogues vulnerabilities. It helps teams predict disruptions and prepare solutions ahead of time. As the Gulf Petrochemicals and Chemicals Association (GPCA)highlights, such libraries are invaluable for spotting weak points across the supply chain and planning tailored mitigation strategies before issues escalate.
Keeping a constant eye on risk factors is crucial for avoiding potential problems. Companies should track key metrics like supplier reliability, inventory levels, and compliance through well-defined KPIs.
Advanced technology, such as real-time analytics tools, can provide actionable insights by analysing market trends and supplier performance data.
Related article: Top Supply Chain Barriers & Proven Strategies to Overcome Them
Navigating global and local regulations is vital to chemical supply chain success. Rules such as the Globally Harmonised System (GHS), REACH, and EPA’s Resource Conservation and Recovery Act (RCRA) are essential frameworks companies must comply with to avoid penalties and ensure safe chemical management.
To manage compliance effectively, organisations should adopt several strategies:
Risk is unavoidable in the chemical industry, but forforward-thinking logistics companies, it’s also an opportunity to gain a competitive edge. Whether diversifying supplier networks, enhancing transport systems, or leveraging advanced compliance tools, success comes from turning challenges into advantages. The real determiner is not about avoiding disruptions but using them as a springboard for innovation and growth.
Businesses must assess their supply chain and identify vulnerabilities. Ask tough questions such as: Where are we most exposed? What steps will strengthen our resilience? The answers lie in proactive planning and bold strategies that don’t just manage risk but transform it into opportunity. Companies that embrace this mindset will thrive and stay ahead.
Leading companies understand that proactive freight risk management is now a key differentiator. By leveraging predictive risk modelling, building flexible infrastructure, and staying ahead of compliance challenges, these companies gain a competitive advantage and ensure resilience in an increasingly unpredictable market.