Lack of equipment, port congestion and employee availability have created a perfect storm for the transportation industry.
The Coronavirus pandemic did more than just disrupt the logistics industry – it laid bare the underlying complexity and fragility of the global supply chain. Pharmaceuticals, with their often specific transport needs, presented unique challenges.
Frank Kilbride, Ireland Country Manager at Aramex, says: “The pandemic led to equipment bottlenecks, increased shipping costs and affected key workers involved in moving pharmaceuticals.”
This was no localised disruption, a short-lived event that could be worked around, but a global event with few countries escaping the turmoil. Moreover, regions experienced waves of coronavirus at different times; one location might overcome a spike in cases, and the associated sick leave and quarantining to begin dealing with the cargo backlog, only to be hampered by virus surges elsewhere. Aramex Ireland’s pharmaceutical customers exporting to the US have endured greatly increased wait times at ports, and have experienced a trebling of inland freight charges as the availability of truck drivers has been greatly reduced.
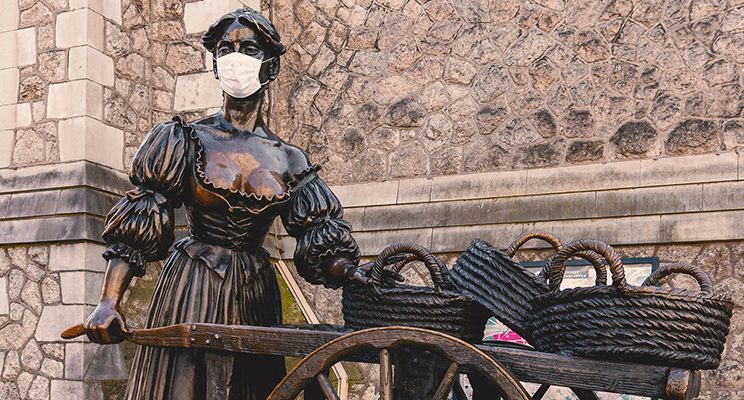
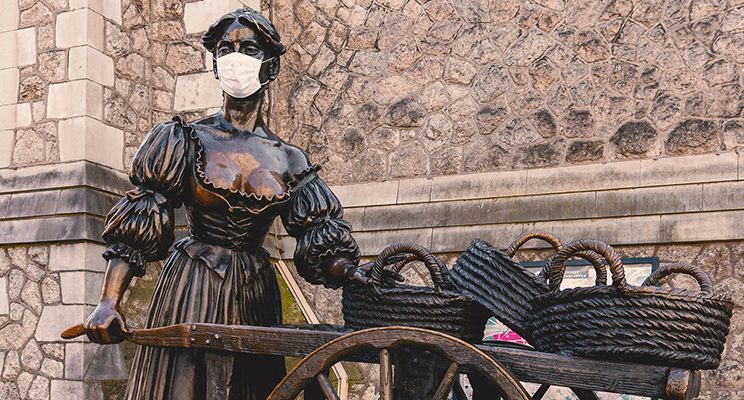
Equipment shortages
Frank Kilbride explains: “The pandemic also exacerbated an already difficult situation with shipping equipment.” This was a particular issue for pharmaceuticals which typically require temperature- refrigerated shipping containers. “Major disruptions such as this slow everything down and that has tremendous knock-on effects because it affects equipment utilisation,” he adds.
Demand for pharma and food goods requiring temperature-controlled equipment has remained consistent throughout the pandemic. However, with extra demand for the movement of vaccines, together with equipment capacity being reduced in the system, freight rates have skyrocketed.
Compounding this issue was the fact that during the uncertainty of the initial stages of the pandemic global demand for goods sharply declined worldwide. In response to this, shipping lines reduced sailings and capacity on their networks.
Rethinking manufacturing
Logistics issues have also forced a worldwide rethink about where the active pharmaceutical ingredients used in medicines and vaccines are manufactured, and the distances and time involved, states Frank Kilbride. He says that governments will need assess how they can work together to build more resilience into the supply chain and, in the longer term, reassess the nature and places of manufacture.
The European Fine Chemicals Group’s (ECFG) Commercial KPI report Dec. 2020 states – “European direct and indirect dependency from Asia, in terms of both APIs and precursors, is estimated to be around 74% of total market volume (in kg).”
The reshoring of API production has already begun in France with Sanofi, Seqens, and UPSA recently combining, with the support of the France Relance programme, to launch a project to build Europe’s only paracetamol production facility in Roussillon, France.