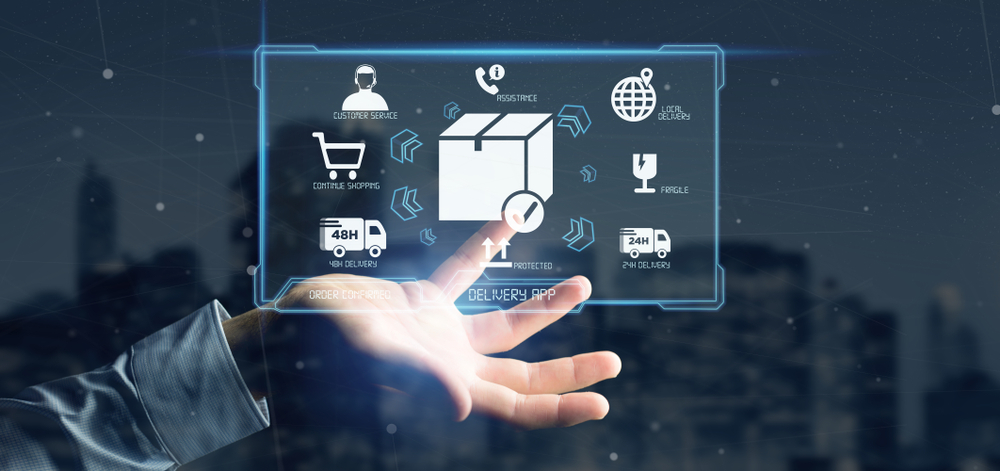
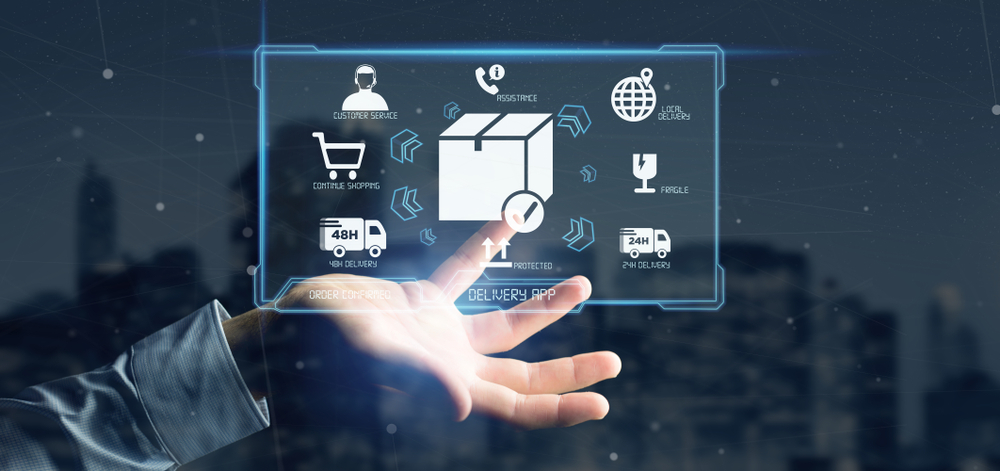
Reverse logistics has become a crucial aspect of the supply chain, and companies that have successfully integrated it have gained a significant competitive advantage in their respective industries. The reverse logistics process is the backward flow of products from the end consumer, or point of sale, back to the production or manufacturing origin.
There are diverse reasons reverse logistics occurs, including defects, damage, failed delivery services, and B2B returns of unsold products for resale. Regardless of the cause, having a properly structured logistics solution provider and supply chain will make the process smooth and seamless.
Why Effective Reverse Logistics Management Matters?
Despite the unwanted reverse process, businesses that successfully instate an effective reverse logistics policy and process stand out from the competition. Here are some of the benefits of having this structure available in a supply chain:
Customer retention: If a customer feels dissatisfied with your product, it is essential to pinpoint the error and make things right to retain them and avoid future complaints.
Reduced cost: A well-structured return process will help you minimise expenses such as administration, technical support, and shipment costs.
Enhanced product life cycle: An item no longer in use can be recycled, repaired, refurbished and resold to increase its product cycle and utility.
Improved public trust: Earning public trust through structured reverse logistics helps build consumer trust, an essential factor in today’s competitive environment.
Related article: Fashion Logistics: Innovating for Speed and Sustainability
What Makes Reverse Logistics Management Successful?
Product returns process
Efficient product returns management is a fundamental aspect of reverse logistics. It should involve determining the appropriate disposal options, including deciding whether to refurbish, resell, repackage, or dispose of the item, streamlining the reverse flow process, and reducing the return shipping costs.
Remanufacturing and refurbishment
Remanufacturing entails disassembling, rebuilding, and repairing products to prepare them for resale, whereas refurbishment involves cleaning, redecorating, and re-equipping items to restore usability. This process should minimise repair, courier and other logistics costs.
Recycling and disposal
Recycling is the process of transforming products into raw materials that can be used to create entirely new products. This process promotes sustainability and reduces the necessity of acquiring new materials, thereby minimising waste and environmental harm.
Inventory management
Effective inventory management is crucial for companies to monitor stock levels and identify optimal order quantities at the correct times. It helps minimise stockouts and quickly highlights items that need to be restocked. By integrating inventory management with reverse logistics, companies can ensure faster and more accurate return processing, which leads to greater cost efficiency and increased customer satisfaction.
Strategies for Optimising Reverse Logistics
Streamlining Product Returns
Streamlining product returns is essential to getting the best out of reverse logistics. It helps the supply chain save time and costs, reduce waste, and improve output. Focus on making returns easy for customers with efficient delivery services and minimal steps that ensure a seamless experience.
Implementing Efficient Remanufacturing Processes
Remanufacturing involves restoring the functionality of high-value end-of-life products. However, due to the unpredictable nature of the reverse material flow, implementing an efficient remanufacturing reverse logistics process can be complex. An efficient remanufacturing process should encompass the collection (or recovery) process, detection or evaluation classification, disassembly and cleansing, remanufacturing, and redistribution.
Sustainable Recycling and Disposal Methods
The accumulation of industrial and commercial waste and the pollution it produces have led to significant environmental damage. Establishing a responsible waste disposal system is essential to improving sustainable reverse logistics. This approach can reduce waste, enhance recycling efforts, and extend product lifespans.
Utilising Technology for Improved Inventory Tracking
Businesses can utilise advanced technologies such as real-time cargo tracking, barcode systems, cloud-based solutions, automated ordering processes, and data analytics to enhance inventory management and facilitate quicker, more informed decision-making. Additionally, it is crucial to establish a clear inventory policy and ensure that employees are well-trained to support the reverse logistics process.
Related article: Innovative E-commerce Solutions: Smart Warehousing Insights
Challenges and Solutions in Reverse Logistics Management
A well-optimised reverse logistics system can significantly enhance supply chain transparency. However, businesses often need help in this area. Understanding and addressing these challenges is crucial for maintaining an efficient and cost-effective supply chain.
Here are some of the top challenges—and solutions—in reverse logistics management.
Managing Customer Returns
The customer returns process is delicate. In fact, some customers order several products intending to return many of them—a practice known as bracketing. A report from Insider Intelligence shows that 63% of customers involved in a survey claimed to have bracketed their purchases. This practice is highly pronounced in the fashion industry, especially where customers are unsure about product sizing.
Solution: Streamline the customer return process, prioritise customer experience, automate returns management, and ensure consistent analysis of returns data.
Balancing Costs and Efficiency
While having a flexible return policy boosts customer loyalty, it can also increase operational costs. The challenge is balancing efficiency and profitability without compromising the goal.
Solution: Implementing advanced technologies such as AI and machine learning can optimise operations by predicting return patterns and automating processes. Additionally, integrating real-time data analytics can provide deeper insights into cost drivers and inefficiencies, enabling more informed decision-making.
Lessons Learned and Best Practices from Industry Leaders
Reverse logistics boost customer satisfaction and retention by refining product quality and design through curated feedback. Refurbishing, remanufacturing, and reselling help reduce environmental impact and extend product lifespans. To achieve these benefits, industry leaders have adopted several best practices, including:
- Integrating a straightforward customer returns process.
- Employing cargo tracking solutions throughout the reverse supply chain process.
- Streamlining data aggregation to determine the costs involved in the return process.
- Repairing, refurbishing, reselling, and recycling defective products.
- Evaluating the shipment and the logistics solution provider to ascertain whether parcels have the correct packing.
- Leveraging technology to ensure seamless processes at every stage.
Key Takeaway
The reverse logistics process involves managing products returned from customers at every level of the supply chain to the manufacturer or distributor. The flow in the logistics solution provider’s journey is particularly pertinent to boosting customer satisfaction, reducing costs, enhancing the product life cycle, reducing waste, and minimising environmental damage. Future trends impacting reverse logistics include reducing the carbon footprint, improving customer satisfaction, and streamlining operations.
Optimise your supply chain with Aramex’s expert reverse logistics services. Contact us now!